1. OVERVIEW
Metal injection molding (MIM) is a typical product of cross-disciplinary, integrating two different processing technologies (plastic injection mold and powder metallurgy). It makes designer get rid of tradition and gets low-cost and heterogenic stainless steel, nickel, iron, copper, titanium and other metal parts via plastic molding. Through this method, designer can have freedom of design.
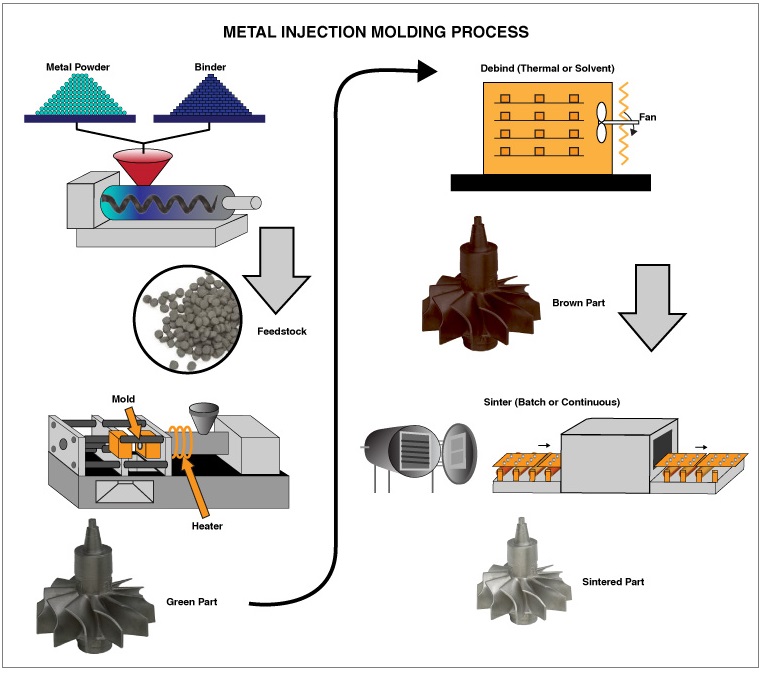
2. PRE-SALES ASSESSMENT
Gian pre-sales team will work closely with you to assess the feasibility for MIM production in terms of cost, material, or manufacturing. Gian will also advise how to change design for achieving the best effect through MIM.
3. RAW MATERIALS
Under the condition of precisely controlled preparation, special metal powder (micron) mixed with high quality polymers in order to get MIM special feeding. Compared to traditional powder metallurgy, particle size of metal powder(micron)and low impurity content assure that MIM sintering density reaches a theoretical density of 98%. Besides, specially formulated multi-polymers are able to provide better liquidity during injecting and can also ensure efficient debinding ability.
4. INJECTION MOLDING
MIM feedstock is heated and filled evenly into mold cavity by injection molding machines, then green components is generated after cooling down. Molds in accordance with the MIM characteristics and reasonable process pairing are the keys to this process.
5. DEBINDING
Major binders in injection components can be gradually and efficiently removed via professional debinding furnace. Remaining binder can maintain the shape of products in order to entering into sintering.
6. SINTERING
In a vacuum furnace or an atmosphere furnace, frame binder can be removed. Metal powder will be densified and transformed into full metal body under the temperature close to the melting point. After cooling, sintering parts are near finished shape.